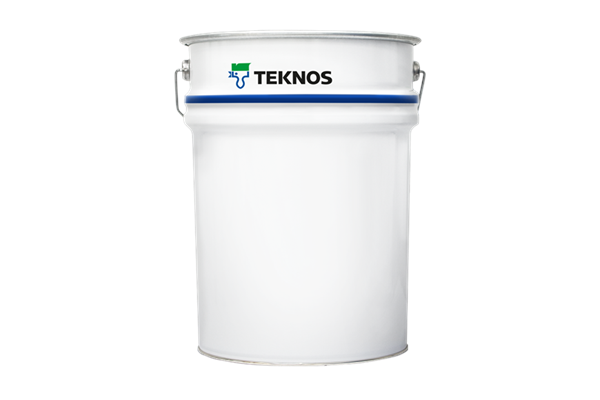
Teknodur Combi 3430-09
About the product
Note these are bases and must be tinted with Tonesystem Teknomix or Teknotint.
TEKNODUR COMBI 3430-09 is a 2-component anti-corrosive pigmented polyurethane paint with a low content of solvents. The hardener used is an aliphatic isocyanate resin. Recommended substrate Steel, Aluminium, Zinc.
Binder Polyurethane.
Used as a 1-coat paint. The paint can also be used as a topcoat in polyurethane systems. Is suitable for surfaces of steel, zinc and aluminium.
The paint provides a high-gloss film with good mechanical properties and good weather resistance. The use of TEKNODUR 0290 polyurethane lacquer is recommended as a clear lacquer when excellent gloss and color resistance is required.
Gloss (60°) Glossy
Hardener Comp. B: TEKNODUR HARDENER 7230
Mixing ratio (A:B) 6:1 parts by volume
Pot life, 23 °C 1 h 30 min
Dilutes more options.
Standard thinner: TEKNOSOLV 9504, TEKNOSOLV 9524, TEKNOSOLV 9526, TEKNOSOLV 9521 or TEKNOSOLV 6220.
Storage The storage stability is indicated on the label. Store cool and dry indoors in tightly sealed packaging. The hardener reacts with humidity, and therefore an opened package should be kept completely closed and used within 14 days.
Pretreatment The surfaces are cleaned of impurities that may be harmful for pretreatment and application. In addition, water-soluble salts are removed by suitable methods. The surfaces of the various materials are pretreated as follows: STEEL SURFACES: Remove scale and rust by sandblasting to degree of cleanliness SA 2½ (standard ISO 8501-1). If the surface is roughened on thin sheets, the adhesion of the paint to the surface is improved.
ZINC SURFACES: Hot-dip galvanized steel structures that are exposed to the weather can be painted if the surface is sandblasted (SaS), so that the entire surface becomes matt. Suitable blowing agents are, for example, aluminum oxide and natural sand. In h.t. According to ISO standard 12944-5, it is not recommended to paint galvanized constructions which are to be immersed in water or soil. When painting such objects, contact Teknos separately. Sandblasting (SaS) is recommended for new galvanized thin sheet constructions. Surfaces that have become dull due to the weather can be treated with RENSA STEEL cleaner.
ALUMINUM SURFACES: The surfaces are treated with RENSA STEEL cleaning agent. Surfaces exposed to the weather are roughened with sandblasting (AISaS) or sanding.
OLD PAINTED SURFACES SUITABLE FOR OVERCOATING: Impurities that can be harmful to the application of the paint (eg grease and salts) are removed. The surfaces must be dry and clean. Old, painted surfaces that have exceeded the maximum paintability must be roughened. Pre-treatment of damaged parts is carried out according to the requirements for surface and maintenance painting.
Choose the place and time for the treatment, taking into account that the pre-treated surface does not become dirty or damp before the subsequent treatment.
Other instructions regarding pre-treatment of the surface can be found in the standards EN ISO 12944-4 and ISO 8501-2.
Application method Airless spraying, Conventional spraying
Application Take into account the pot life of the mixture when calculating the amount to be mixed at one time. Before application, base and hardener are mixed in the right ratio. Carefully stir down to the bottom of the container. Inadequate stirring or incorrect mixing ratio results in insufficient curing and poorer film properties.
Stir thoroughly before use. Spray gun and container are cleaned before use with a thinner suitable for the paint.
Suitable airless nozzle size. 0.013 - 0.017"
Application conditions The surface to be treated must be dry. During application and drying, the temperature of the air, the surface and the product must be above +5 °C and the relative humidity below 80%. In addition, the temperature of the surface to be treated and the product must be at least +3 °C above the dew point of the air
Thinning If necessary, thin the paint with TEKNOSOLV 9504 (standard thinner), TEKNOSOLV 9524 (slow thinner) TEKNOSOLV 9526, TEKNOSOLV 6220 or TEKNOSOLV 9521
Do not use common thinners as they may contain alcohol which will react with the hardener
Drying time +23°C / 50% RH (dry film 80 μm) - dust dry 45 min (ISO 9117-3:2010) - non-adhesive 5 h (ISO 9117-5:2012) - fully cured 7 days. See technical data sheet for further information.
The hardener and the finished mixture contain isocyanates. In poorly ventilated rooms and especially when spraying, the use of a fresh air mask is recommended. For short or temporary work, a mask with an A2-P2 filter can be used. In this case, eyes and face must be protected. The hardener should be opened with care, as excess pressure may occur during storage.
- Industries: Industrial Metal Finishing
- Brand: Teknos
- Supplier item no.: 7400603010
Safety and enviroment
GHS


Safety and enviroment
GHS


Safety and enviroment
GHS


Safety and enviroment
GHS


Safety and enviroment
GHS

